Introduction to Heat Exchangers
Heat exchangers are designed to exchange heat between two or more fluids. The heat transfer process can be liquid to liquid, liquid to gas or gas to gas. Depending on the type of heat exchanger, fluids may be separated or directly contacted.
Heat exchangers used in a wide range of industries for cooling and heating purposes. And also, heat exchangers can apply for the energy conservation, by transferring heat from a system where it is not needed for another system where it can be effectively used. Chemical plants, petrochemical plants, petroleum refineries, sewage treatment, power stations, space heating, air conditioning, natural gas processing, and refrigeration are some applications where heat exchangers operated.
Heat exchangers designed or selected for a process by considering several factors such as application, operational specifications, characteristics of thermal fluids, the material of construction, space constraint, scalability, environment, and cost.
Flow Arrangements in Heat Exchanger
Flow arrangement depends on the direction of the movement of fluids within the heat exchanger relative to each other.
There are four flow arrangements in heat exchangers.
- Co-current
In co-current flow heat exchangers, fluids move parallelly and in the same direction as each other. The co-current flow arrangement facilitates the highest thermal uniformity across the walls of the heat exchanger. Co- current heat exchangers have comparatively lower efficiencies than counter-current heat exchangers. - Counter-current
In counter-current flow heat exchangers, fluids move parallelly but in the opposite direction as each other. This flow configuration allows the highest amount of heat transfer between fluids. Thus this flow arrangement has the highest efficiency than alternative flow configurations. - Cross Flow
Crossflow heat exchangers allow fluids to flow perpendicularly to one another. The efficiency of the cross-flow heat exchanger lies between the that of counter-current and co-current heat exchangers. - Hybrid
Hybrid heat exchangers have combined flow arrangements—for example, both cross flow and counter flow arrangements designed within a single heat exchanger.
Types of Heat Exchangers
Shell and Tube Heat Exchanger
Shell and tube heat exchanger is most popular in the industry. This heat exchanger consists of a tube bundle which housed within an outer cylindrical shell. Both tubes and the shell made out of thermally conductive material. Two fluids can exchange heat via one fluid flows through the pipes, and other fluid flows outside of the pipes within the shell. Both the shell side and tube side have inlet and outlet for each. Baffles used to induce turbulent mixing in the shell side, which leads to enhance convection. The flow configuration can be co-current, counter-current, or cross-flow according to the requirements.
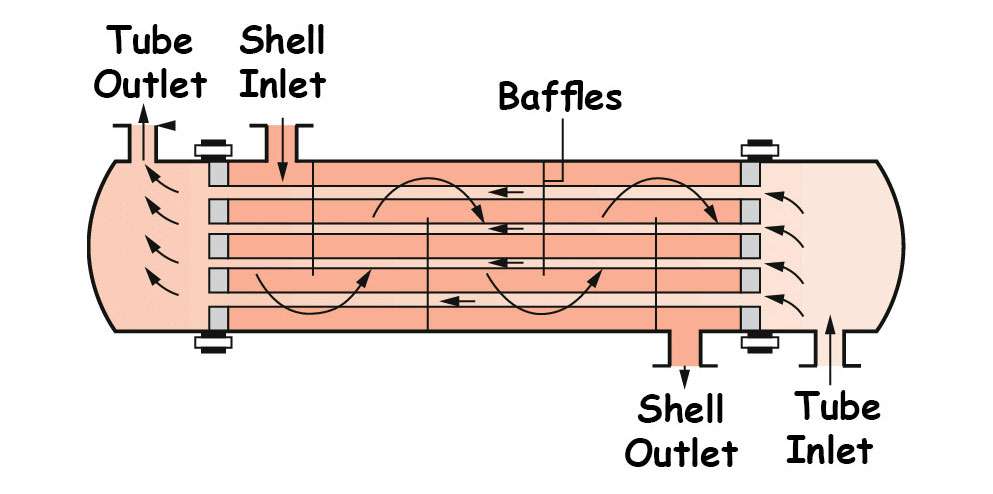
Shell and tube heat exchangers are famous because of the simple design, robust characteristics, relatively low purchase cost, and maintenance cost. This heat exchanger has a very high heat transfer rate but comparatively more space than a plate heat exchanger, which has the same thermal exchange capacity.
Plate and Frame Heat Exchanger
Plate and frame heat exchangers are commonly utilized in the industry. It consists of a series of parallel corrugated plates on a frame, which allows the creation of a channeling series for fluids to flow. A plate always contacted on one side with cold fluid and the other side with hot fluid. Corrugations on the plates enhance heat transfer.
This configuration is more advantageous because fluids exposed to a larger surface area since fluids spread over the plate. Two fluid streams flow counter currently within the heat exchanger. The hot fluid flows down one plate and whereas the cold fluid flows up the next plate.
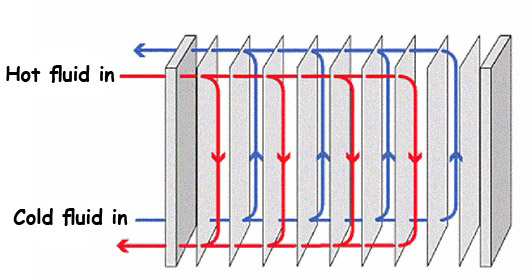
There are inlets and outlets at the corners of the plates—these ports sealed by gaskets around the ports. And also, there are gaskets along the plate edges. This prevents the mixing of two fluids. Having a high heat transfer coefficient and a high fouling resistance are definite advantages of the plate heat exchanger. Generally, plate and frame heat exchangers are most suitable for the heat transfer between medium or low-pressure fluids.
Plate heat exchangers have high adaptability because the required heat transfer area can achieve by increasing or decreasing the number of plates. And also, since this type has a compact structure, it requires less space compared to other heat exchangers with the same thermal exchange capacity. Cleaning and repairing are easy compared to other heat exchangers. But, there can be problems due to poor sealing. And also, the operating temperature limited and depended on the gasket material.
Double Pipe Heat Exchanger
A double pipe heat exchanger is a combination of one pipe inside of another larger pipe. This is the elementary form of a shell and tube heat exchanger. One fluid passes through the pipe while the other fluid flows through the annulus between two pipes. The wall of the inner pipe act as the heat transfer area, which manufactured from a thermally conductive material. Generally, the pipes doubled back multiple times according to the purpose.
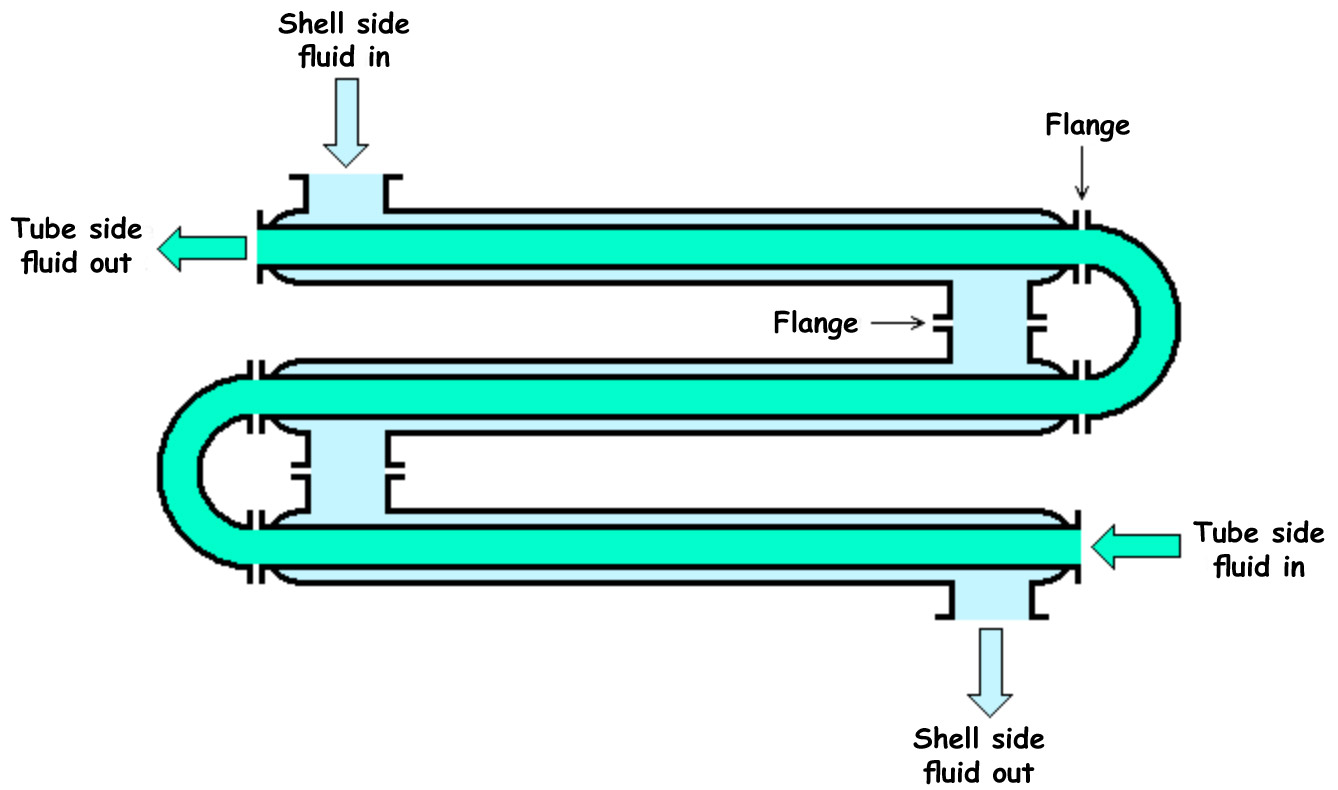
Though the flow configuration of a double pipe heat exchanger can be either co-current or counter-current, it is mostly used in counter current. Counter-current flow is mostly thermally efficient as it increases the system’s heat transfer coefficient. Due to the simple construction and the ability for free expansion, this type can handle relatively high pressures and temperatures.
Spiral Plate Heat Exchanger
The spiral plate heat exchanger has two long flat metal plates wrapped around a center core by creating two concentric spiral flow passages for two fluids. The plate edges welded to prevent flow bypassing or fluid mixing. The gap between plates maintained by welded spacer studs most of the time. Although counter-current flow pattern generally used, can also apply co-current flow configuration.
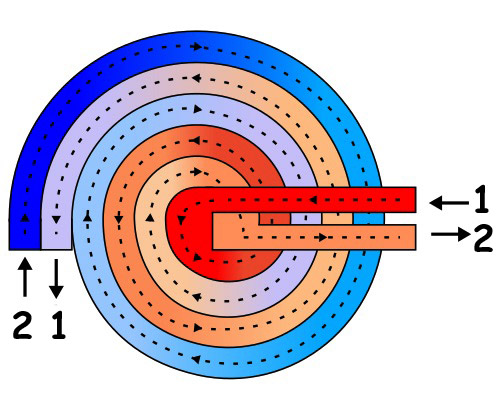
Spiral plate heat exchangers have advantages due to inherent circular design and large surface area to volume ratio. It has high thermal efficiency. And also, it has a self-cleaning effect, which reduces fouling, thereby suitable to handle fluids like process slurries, sludge, and fluids with suspended solids. Another advantage is that this requires minimal space for the installation and maintenance due to its compact structure